The most important factors in choosing a laser system are laser output power and beam quality.
- Power determines processing efficiency: Higher power means faster processing speed and greater penetration depth.
- Beam quality determines processing precision: Higher beam quality results in smaller focused spots and greater depth of focus, thereby improving precision.
- The two factors are interrelated: Power and beam quality are not entirely independent and can influence each other. For example, increasing power may lead to a decrease in beam quality. When selecting a laser system, it is essential to consider both power, beam quality, and other related factors to choose the most suitable laser. Only by doing so can the best processing results be achieved in practical applications.
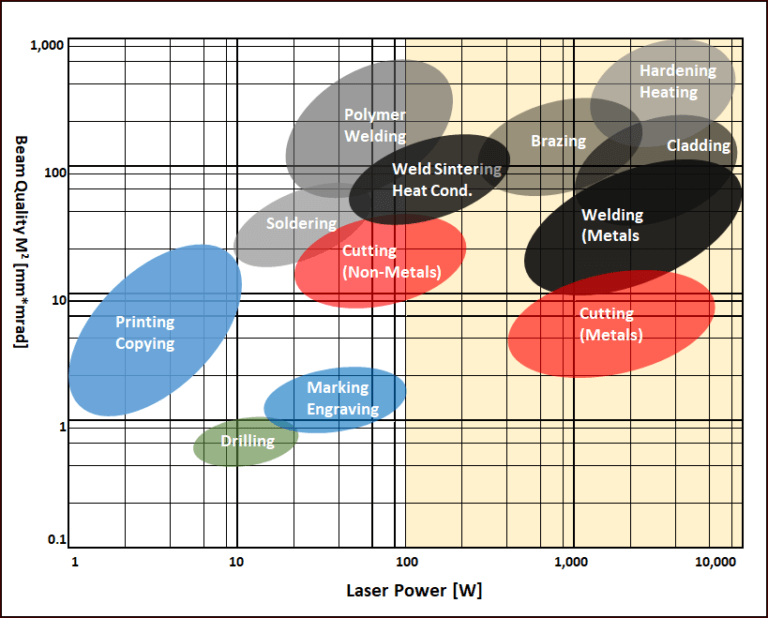
1. Laser Power
1.1 Average Power
Average power refers to the mean optical power output by a laser over a unit of time, typically measured in watts (W). It can be directly measured using a power meter or calculated using an energy meter in conjunction with the pulse repetition frequency.
- Continuous lasers: Average power determines the thermal effect and material removal rate. Higher power leads to faster processing, but it can also increase the heat-affected zone.
- Pulsed lasers: Average power determines the amount of processing per unit of time. With the same pulse energy, a higher repetition rate results in higher average power.
1.2 Peak Power
Peak power refers to the maximum instantaneous power during a laser pulse, also typically measured in watts (W). Peak power cannot be directly measured but can be calculated by measuring the pulse waveform with a high-speed photodetector or using an autocorrelator to measure pulse width combined with pulse energy.
- Pulsed lasers: Peak power determines the material removal mechanism. High peak power is conducive to generating plasma and achieving efficient material removal.
- Ultrafast lasers: Peak power determines the strength of nonlinear effects, such as multiphoton absorption and plasma formation.
Parameter | Application Process | Impact Factors |
---|---|---|
Average Power | Cutting, Welding, Drilling, Surface Treatment | Processing speed, heat-affected zone, material removal rate |
Peak Power | Micromachining, Marking, Drilling, Film Removal | Material removal mechanism, nonlinear effects, damage threshold |
1.3 Application Examples
- Cutting: Requires high average power and appropriate peak power to ensure cutting speed and quality.
- Welding: Deep-penetration welding requires high average power, while for thin sheet welding, peak power must also be considered.
- Drilling: High peak power is needed to quickly generate vaporized holes.
- Marking: High peak power and beam quality are required for clear marking.
- Micromachining: In ultrafast laser micromachining, peak power determines the strength of nonlinear effects, which in turn affects processing precision.
2. Laser Beam Quality (M² Value)
2.1 What is M² Value?
The M² value is a key parameter used to describe laser beam quality—specifically, its divergence characteristics and focusing ability. It indicates how closely a laser beam resembles an ideal Gaussian beam. The ideal Gaussian beam has an M² value of 1, while actual laser beams typically have M² values greater than 1. The closer the M² value is to 1, the better the beam quality, with smaller divergence angles, smaller focus spots, and higher energy concentration.
2.2 How to Measure M² Value?
Measuring the M² value typically requires a specialized laser beam quality analyzer, which measures the beam waist radius and divergence angle at different positions and calculates the M² value using specific algorithms.
The measurement process generally involves the following steps:
- Preparation: Collimate the laser beam to ensure stability.
- Data Collection: Pass the laser beam through the analyzer, which automatically collects intensity distribution data at different positions.
- Data Processing: The analyzer software calculates the M² value based on the collected data using fitting methods.
2.3 The Role of M² Value
The M² value can be used to characterize both the initial output beam quality of the laser and the beam quality after external optical reshaping.
- Initial output beam: The M² value reflects the design and manufacturing quality of the laser and is an important performance indicator.
- After external optical reshaping: By comparing the M² values before and after reshaping, the effectiveness of the optical system can be evaluated. If the M² value increases after reshaping, it indicates that the external optics have reduced the beam quality.
A lower M² value is crucial for many laser applications. For example:
- Laser processing: A lower M² value results in a smaller focus spot, leading to higher processing precision.
- Laser measurement: The M² value affects the resolution and sensitivity of the measurement system.
However, poor beam quality with a higher M² value can also be advantageous in some applications:
- Large-area uniform heating: A higher M² value results in a larger divergence angle and more uniform energy distribution, which is useful in processes like copper welding or steel surface hardening.
- Deep-penetration welding: Poor beam quality can provide a wider heat-affected zone, aiding in melt pool formation and improving weld quality.
- Reduced alignment accuracy requirements: A beam with lower quality requires less stringent alignment, simplifying the process and increasing processing speed.
Typical applications include laser copper welding, plastic plate welding, steel surface hardening, and sintering of large-area workpieces.
2.4 Typical M² Values
In general, lasers are designed to optimize beam quality, with M² values as close to an ideal Gaussian beam (M² = 1) as possible. Lasers used in marking and engraving, or for precision cutting, typically have M² values below 1.5, sometimes as low as 1.1. Lasers used for large workpiece cutting and welding, such as multi-mode lasers, often have M² values greater than 2, reaching 5, 10, or higher.
2.5 How to Adjust M² Value
- Custom Laser: Collaborate with the laser manufacturer to customize a laser with specific parameters by adjusting internal optical components, such as mirrors or gratings, to modify the beam mode and M² value.
- External Optical Design: Compared to the high cost, long cycle time, and low maturity of custom lasers, external optical adjustment is the common method for modifying M² values.
Common components for reducing M² value:
- Spatial filters: Use diffraction through a small aperture to filter out high-frequency spatial components and reduce beam divergence.
- Apertures: Restrict beam transmission to remove edge diffraction and distortion.
- Aspheric lenses: Compensate for spherical aberrations and improve focusing characteristics.
- Diffractive optical elements (DOE): Modulate the wavefront to achieve beam shaping, such as flat-top or ring-shaped beams.
- Adaptive optics systems: Measure and correct wavefront distortions in real-time, often used in high-power laser systems and optical communications.
Components to increase M² value:
- Fiber bundles: The incoming beam is coupled through a randomly arranged fiber bundle, resulting in beam scattering.
- Frosted glass: The microstructure on the glass surface scatters the beam.
- Diffusers: Lens surface microstructures cause beam divergence to achieve uniform beam distribution.
- DOE: Modify the beam’s phase to alter its wavefront for beam homogenization or splitting.